[Pipe mill production line with welding and cutting functions]Innovative Advancements in Pipe Mill Production Lines Featuring State-of-the-Art Welding and Cutting Functions for Enhanced Efficiency
News 2024-10-7
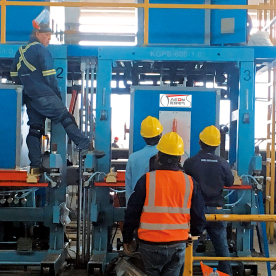
Innovative Advancements in Pipe Mill Production Lines Featuring State-of-the-Art Welding and Cutting Functions for Enhanced Efficiency
In the manufacturing world, the demand for high-quality pipes used across various industries is growing at an unprecedented rate. A well-designed pipe mill production line plays a vital role in meeting this demand efficiently. With the integration of advanced welding and cutting functions, modern pipe mill production lines are revolutionizing the way pipes are produced, offering enhanced efficiency, precision, and quality.
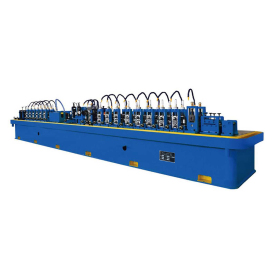
Innovative Advancements in Pipe Mill Production Lines Featuring State-of-the-Art Welding and Cutting Functions for Enhanced Efficiency
Electric Resistance Welding (ERW) is particularly noteworthy because it utilizes electrical resistance to generate heat and fuse the pipe seam. This technique not only speeds up the production line but also ensures uniform weld quality. The system can be easily integrated with a robust automation framework, allowing for real-time monitoring and adjustments, which leads to reduced labor costs while increasing production output.
On the other hand, submerged arc welding is ideal for creating strong, high-quality welds in larger diameter pipes. This type of welding is conducted while the arc is submerged under a layer of flux, allowing for deep penetration and exceptional bond strength. The infusion of this technology into pipe mill production lines means manufacturers can produce pipes that meet or exceed stringent industry standards, making them suitable for critical applications in sectors like oil and gas, construction, and infrastructure.
The cutting functions integrated into the pipe mill production line are equally essential. Accurate cutting ensures that the finished pipes meet specified lengths and dimensional tolerances, which is vital in applications that require high precision. Advanced cutting techniques, such as laser and plasma cutting, offer unparalleled accuracy and speed. These technologies allow for complex cuts, which can be particularly beneficial for custom projects and specialty piping applications.
Moreover, the automation of cutting functions reduces human error and increases safety within the production environment. Automated cutting systems can be programmed to execute a variety of cuts without the need for manual intervention, leading to consistent quality across all produced pipes. As a result, manufacturers are better positioned to meet customer demands while minimizing wastage and maximizing output.
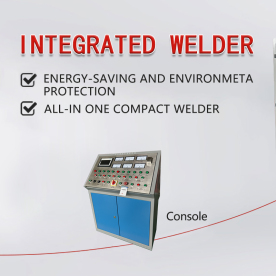
Innovative Advancements in Pipe Mill Production Lines Featuring State-of-the-Art Welding and Cutting Functions for Enhanced Efficiency
Additionally, advancements in technology mean that these production lines are increasingly connected, allowing for data collection and analysis. Through the Internet of Things (IoT), manufacturers can gain actionable insights into their operations. Monitoring overall equipment effectiveness (OEE) can help identify bottlenecks, reduce downtime, and facilitate predictive maintenance; which translates into significant cost savings.
Sustainability is another pressing concern for modern pipe manufacturers. The latest pipe mill production lines are increasingly designed with energy-efficient technologies, reducing the overall carbon footprint of production processes. Improved thermal management and the use of recyclable materials are also part of the sustainability narrative, marrying ecological responsibility with economic efficiency.
In conclusion, the integration of welding and cutting functions in pipe mill production lines is transforming the manufacturing landscape. By leveraging advanced welding techniques, precision cutting technologies, and IoT capabilities, manufacturers can produce high-quality pipes efficiently while minimizing their environmental impact. As industries continue to evolve and demand for pipes rises, these advanced production lines are poised to become the backbone of modern manufacturing, driving innovation and excellence in the field. By investing in such technologies, manufacturers not only enhance their competitive edge but also pave the way for a more sustainable future.