[Precision Tube making equipment]Exploring the Advancements and Applications of Precision Tube Making Equipment in Modern Manufacturing Processes
News 2024-10-7
Precision tube making equipment has emerged as a cornerstone of modern manufacturing, enabling industries to produce high-quality tubes with unparalleled accuracy and consistency. This specialized machinery is designed to create tubes that meet specific dimensional requirements and tolerances, serving a myriad of applications across various sectors, including automotive, aerospace, construction, and medical devices. As industries continue to evolve and demand for precision components increases, understanding the advancements and applications of precision tube making equipment is essential for manufacturers looking to stay competitive.
The Basics of Precision Tube Making Equipment
At its core, precision tube making equipment is a collection of machines and technologies designed to manufacture tubes from various materials, such as stainless steel, aluminum, brass, and plastics. The primary processes involved in tube making include extrusion, rolling, and welding. Each method has its unique advantages, enabling manufacturers to choose the most suitable approach based on their specific requirements.
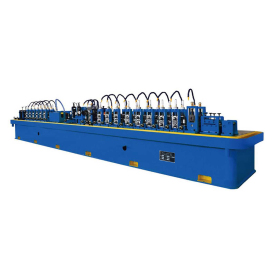
Exploring the Advancements and Applications of Precision Tube Making Equipment in Modern Manufacturing Processes
2. **Rolling**: Rolling is another widely used technique, particularly for the production of seamless tubes. In this process, heated metal billets are passed through rollers to form the desired tube shape. The rolling method is particularly advantageous for large-volume production runs, as it offers high efficiency and reduced material waste.
3. **Welding**: For applications that require longer lengths or specific diameter specifications, welding becomes a critical component in tube making. Various welding technologies, including laser welding, TIG welding, and MIG welding, are employed to create strong, durable joints between sections of tubing. This method is essential for producing tubes that can withstand high pressure and extreme conditions.
Technological Advancements
In recent years, technological innovations have revolutionized the capabilities of precision tube making equipment. The integration of automation, robotics, and data analytics has transformed traditional manufacturing processes into smart production systems, resulting in increased efficiency, reduced downtime, and superior product quality.
- **Automation**: Modern precision tube making equipment often incorporates automated processes, allowing for seamless production lines that can operate continuously with minimal human intervention. Automated equipment can monitor production parameters in real-time, ensuring that any deviations are promptly addressed, leading to a more consistent quality of the finished product.
- **Robotics**: The use of robotics in handling and processing materials has increased significantly. Robots can perform tasks such as loading and unloading material, as well as quality inspections. This not only speeds up the production process but also reduces the risk of human error.
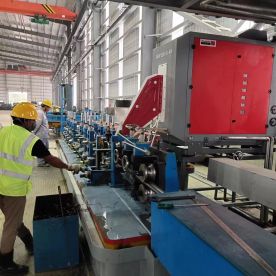
Exploring the Advancements and Applications of Precision Tube Making Equipment in Modern Manufacturing Processes
Applications of Precision Tube Making Equipment
The versatility of precision tube making equipment means that it finds applications across numerous sectors.
- **Automotive**: The automotive industry requires tubes for fuel lines, exhaust systems, and structural components. Precision-engineered tubes are essential for ensuring safety and performance standards are met.
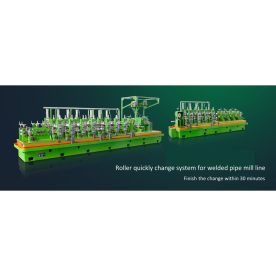
Exploring the Advancements and Applications of Precision Tube Making Equipment in Modern Manufacturing Processes
- **Medical Devices**: In the medical field, precision tubes are used in devices such as catheters and stents. The production of these components requires adherence to strict sanitary and quality standards, making precision tube making equipment indispensable.
- **Construction**: Precision tubes are also widely used in construction for scaffolding, piping, and structural support. The ability to produce durable, high-strength tubes is crucial in ensuring the safety and longevity of construction projects.
Conclusion
As the demand for precision components continues to rise, the role of precision tube making equipment in modern manufacturing cannot be overstated. The advancements in technology, coupled with the versatility of applications across various industries, position precision tube making equipment as a vital component in the production of high-quality tubes. Manufacturers who invest in state-of-the-art precision tube making equipment are not only enhancing their production capabilities but also ensuring that they remain competitive in a rapidly evolving marketplace.